Environmental sustainability and social responsibility are among the fundamental aspects of the manner in which Snam creates value for itself and for its stakeholders, and they therefore represent an integral part of defining strategic and operational corporate choices. Sustainability helps to manage business risks, improve performance and enhance the Companys reputation and intangible assets.
Integrating sustainability and business takes place through planning and control procedures and tools that feed into the cycle of continuous improvement. At the basis of this management system, which has been extended to the entire corporation and is currently undergoing a consolidation phase, there is the periodic updating of “Areas for Improvement of Sustainability”, approved by corporate management in September 2011 and valid for the 2012-2015 period, with the subsequent identification, by different corporate functions, of the initiatives and projects relative to areas to be included in the Corporate Plan. Areas for improvement are grouped into four macro areas: Governance, People, Stakeholder engagement and Environment.
The state of progress of the projects and the achievement of planned goals with their respective targets are monitored by the Snam sustainability function, which is also responsible for preparing reports for stakeholders through the annual publication of the Report and the updating of the content in the sustainability section on the website.
COMMITMENTS AND ACTIONS
Download XLS (20 kB) |
GOVERNANCE |
Areas for improvement |
Actions (2010-2011 and in progress) |
KPI |
In this Report |
Sustainability model |
Ensuring adequate oversight of sustainability issues at all Snam companies, in line with Snam’s governance and guidelines |
|
|
Development and sustainability |
Business ethics |
Updating the Code of Ethics and disseminating the principles set out in the Code (and in Model 231) within the group, developing training courses for staff |
|
|
|
Risk & Crisis management |
Implementing integrated group risk management, including ethical, social and environmental risks |
|
|
Download XLS (22 kB) |
PEOPLE |
Areas for improvement |
Actions (2010-2011 and in progress) |
KPI |
In this Report | ||
| ||||||
Training |
Increasing the wealth of abilities and skills and maintain a high degree of staff involvement |
|
|
|||
Health and safety |
Reducing accident rates through an integrated programme and implementing H&S management systems |
|
|
|||
Valuing people |
Implementing growth tracks and identify specific assessment methodologies based on role and seniority, also taking into account geographic mobility |
|
|
|||
Internal com- |
Implementing communication and interaction tools and carrying out a group-wide climate survey |
|
|
|||
Corporate welfare |
Studying and carrying out initiatives to benefit employees |
|
|
Download XLS (24 kB) |
STAKEHOLDER ENGAGEMENT |
Areas for improvement |
Actions (2010-2011 and in progress) |
KPI |
In this Report | ||
| ||||||
Engagement model |
Actions for involvement by type of stakeholder and enhancing communication with the media |
|
|
|||
Philanthropy |
Defining an overall strategy consistent with business activities and launching initiatives on the subject |
|
|
Community and territory | ||
Communities and Territory |
Implementing actions for dialogue and involvement |
|
|
|||
Institutions |
Defining guidelines on relations with the government |
|
|
| ||
Shareholders |
Increasing information for institutional and retail investors |
|
|
|||
Customers |
Implementing sales process quality, traceability and transparency |
|
|
|||
Suppliers |
Extending sustainability best practices along the supply chain |
|
|
Download XLS (22 kB) |
ENVIRONMENT |
Areas for improvement |
Actions (2010-2011 and in progress) |
KPI |
In this Report | ||
| ||||||
Climate change and energy efficiency |
Limiting greenhouse gas emissions |
|
|
|||
Atmospheric emissions |
Restricting nitrogen oxide emissions |
|
|
Carbon footprint and energy efficiency | ||
Biodiversity |
Integrating biodiversity into the sustainability policy |
|
|
|||
Land recovery |
Reclamation of sites contaminated by previous industrial activity |
|
|
|||
Water |
Reducing draws and optimising water discharges |
|
|
|||
Waste |
Increasing waste sorting and recycling |
|
|
|||
Noise emissions |
Mitigating emissions from the most exposed facilities |
|
|
|||
Landscape |
Reducing the visual impact of infrastructure |
|
|
|
Management systems
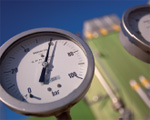
Snam adopts specific certified management systems with the objective of ensuring that corporate processes and activities meet the required standards on worker health and safety, environmental protection and the quality of the services offered.
The table shows the various management system certifications and laboratory accreditations obtained.
In 2011, Snam Rete Gas obtained the certification of compliance with UNI-EN-ISO 9001 quality management system standards for the process of defining network transportation capacity. The inspections, conducted by DNV, were completed with a favourable outcome in May, confirming the Company’s attentiveness to process quality, transparency and traceability.
In order to verify the application and effectiveness of the management systems adopted, identify opportunities for improvement and verify legal compliance, periodic audits are systematically planned and performed. During the year, 359 audits were performed (including 313 internal audits by specialised staff and 46 by external companies). In addition, all of the activities necessary for maintaining and renewing existing certifications were implemented.
Specifically, we note that at the end of the year the environmental management systems certified according to the ISO 14001 standard for the gas compression stations and gas pipeline networks of Snam Rete Gas, verified by the certifying entity, were integrated into a single management system. Therefore, starting in 2012, a single certification will be implemented.
For 2012 the main objectives are:
- extend certification of worker health and safety management systems in accordance with the OHSAS 18001 standard to the entire Snam group;
- plan activities at Snam Rete Gas to extend the environmental management system in accordance with the ISO 14001 standard to the whole company.
Download XLS (20 kB) |
Company |
Field of application |
Type of certification and accreditation |
Year of initial certification |
Snam Rete Gas |
Compression stations (11 facilities) |
ISO 14001 |
2001 |
Snam Rete Gas |
Gas pipeline network (8 districts, 54 maintenance centres, and 32,010 km of gas pipelines) |
ISO 14001 |
2008 |
Snam Rete Gas |
Dispatching of natural gas |
ISO 9001 |
2003 |
Snam Rete Gas |
Natural gas metering service, transportation network, and management of the design and construction of metering apparatus |
ISO 9001 |
2009 |
Snam Rete Gas |
Company |
OHSAS 18001 |
2010 |
Snam Rete Gas |
Defining network transportation capacity |
ISO 9001 |
2011 |
Snam Rete Gas |
Calibration of natural gas mixtures |
ISO 17025 (ACCREDIA) |
2002 |
Snam Rete Gas |
Piped gas flow emissions analysis tests |
ISO 17025 (ACCREDIA) |
2007 |
STOGIT |
Company |
ISO 14001 |
2002 |
STOGIT |
Natural gas metering and accounting service |
ISO 9001 |
2008 |
GNL Italia |
Regasification plant |
ISO 14001 |
2000 |
ITALGAS |
Company |
ISO 14001 |
2001 |
Napoletana Gas |
Company |
ISO 14001 |
2003 |