Accident prevention
Preventing accidents, which is the main aim of health and safety, takes place through targeted action to eliminate or reduce the typical risk factors associated with working activities.
In-depth accident analysis is designed to identify any measures to eliminate, mitigate and correct risk factors, by applying technical and management organisational solutions to equipment, plants and workplaces, as well as operational and behavioural procedures.
The actions and results arising from the accident survey are explored in detail during regular safety meetings, where employees are informed about accident causes and any preventative and protective measures adopted.
Improvement and prevention plans focused on reducing accidents have mainly involved structured actions for informing the personnel and raising their awareness, to promote safe and responsible conduct, adherence to operating and safety procedures and the proper use and maintenance of work equipment and protective devices.
In addition to these plans, plant and safety equipment, systems and devices are maintained and checked by both internal staff and by external entities or qualified external firms.
This ensured that the number of accidents among employees was limited: a good performance was achieved, with 15 accidents (the same number as in 2012) and no fatalities. As the total number of hours worked was the same as in 2012, the frequency index was also identical to the previous year (1.51), while the severity index was 0.09 (+50%), indicating that the nature of the events had more significant consequences.
Download XLS (22 kB) |
Accidents at work (no) |
|||
|
|
|
|
|
2011 |
2012 |
2013 |
Total employee accidents |
22 |
15 |
15 |
Total contractor accidents |
78 |
27 |
22 |
ACCIDENTS AT WORK (NO)
Employee frequency index
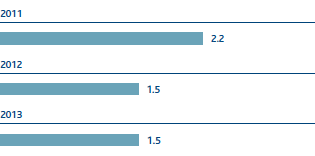
Number of non-commuting accidents with incapacity of at least one day, per million hours worked.
ACCIDENTS AT WORK (NO)
Employee severity index
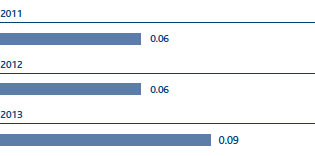
Number of working days lost (calendar days) in relation to noncommuting accidents with incapacity of at least one day, per thousand hours worked.
The commitment to training continued, in line with previous years. All health and safety courses were organised and delivered in compliance with the agreement of 21 December 2011 between central and regional governments. Relevant technical and professional training is conducted in classrooms and on the job, favouring in-house teaching from experts and, where appropriate, collaborating with external training institutions and organisations of excellence.
CAUSES OF EMPLOYEE ACCIDENTS
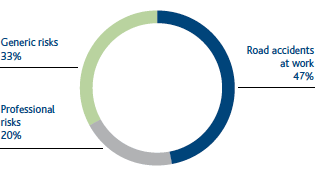
Download XLS (22 kB) |
Health and safety training (no) GRI - G4: LA9 |
|||
|
|
|
|
|
2011 |
2012 |
2013 |
Hours provided |
28,563 |
26,959 |
34,641 |
Attendance |
4,452 |
4,062 |
4,255 |
Download XLS (23 kB) |
A zero-accident (*) year GRI - G4: LA6 |
|||
|
|
||
Company |
Homogenous group |
||
|
|||
Snam Rete Gas |
Central Eastern District, Central Western District, Operations (S. Donato site), Investment Project Creation, South Eastern District, Staff Site (P-AD-SUPC-PAC) |
||
Italgas |
North District, Sicily District, South Distribution Networks Project, Central District, North-West District, South District |
||
Stogit |
Clusters of Minerbio – Sabbioncello, Sergnano – Ripalta, Brugherio – Settala, Cortemaggiore – Bordolano and Crema Operating Site |
||
Gnl Italia |
All companies (2 homogenous groups) |
At the same time, the launch of initiatives involving suppliers, and the constant and progressive raising of supplier awareness of the need to adopt best practice, led to positive improvements in health and safety management during subcontracting activities.
Particular attention is paid to supplier qualification and subsequent assessment, using a feedback model and specific inspection procedures conducted as work is being performed.
The supplier accident indices, which are also taken into account in the supplier qualification assessment, recorded a marked decrease in the frequency index (-38%) and in the severity index (-45%) in 2013.
ACCIDENTS AT WORK (NO)
Contractor frequency index
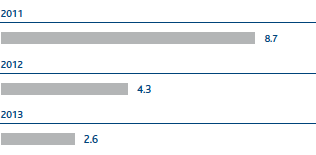
Number of non-commuting accidents with incapacity of at least one day, per million hours worked.
ACCIDENTS AT WORK (NO)
Contractor severity index
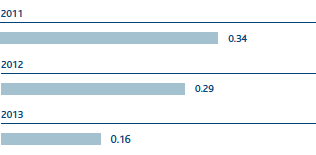
Number of working days lost (calendar days) in relation to noncommuting accidents with incapacity of at least one day, per thousand hours worked.
“Make comparisons to prevent and improve”
This is a workshop that focuses on building shared value between the Company and its suppliers.
It involves sharing best practice, joint analysis of critical areas in the management process for HSE matters, activation of continuous improvement processes and widespread diffusion of a culture of safety and environmental protection. These are the targets for the third edition of the programme, which was launched by Snam in 2011 with the “Supplier’s Day for Sustainability” initiative, and repeated in 2012 with an employees’ day addressing the subject “My safety is your safety”.
Special attention was paid to the importance of those suppliers that the Snam Group regards as primary stakeholders. The Group aims to implement the strategic plan and carry out action to maintain its assets with these stakeholders, in the interests of interacting with each other and making continual comparisons so that quality of service can be enhanced and a continuous improvement approach ensured for HSEQ services.
Some new initiatives developed by Snam were presented during the event, designed to make its supply chain increasingly efficient. These included the new vendor rating model, designed to implement service quality, creation of the Safety Trophy to reward subcontractors that invest in safety and achieve outstanding performance, and the supplier portal, the new platform designed to manage supply chain processes more efficiently and to create an IT networking system that is better organised, to share good practices and awareness from a “shared value” perspective.
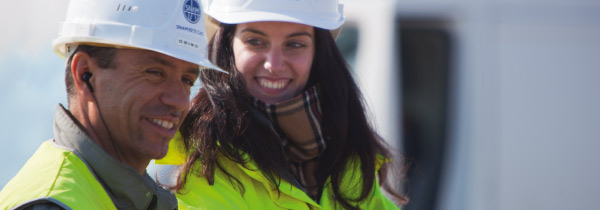