Keeping our human capital safe GRI - G4: LA6, LA9
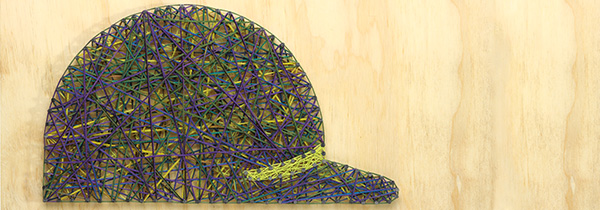
Over the years, Snam has managed to reduce the number and severity of accidents suffered by its employees and contractors. We are focused on workplace safety to the extent that bonuses awarded to our managers and executives depend partly on meeting targets in this area. In spite of this, in 2015 there were three fatal incidents involving our employees: one during an inspection to find a gas leak in a city centre, one during work on a gas distribution pipeline and one following a sudden illness that can probably be attributed to natural causes. There was also one fatal road accident during an employee’s commute.
Thanks to our stakeholder engagement efforts and monitoring and awareness-raising initiatives, we managed to reduce the supplier accident frequency index by 27% compared with 2014 and keep the severity index at a low level.
Management strategies |
Actions |
Centralising operating systems |
In 2015, we continued to implement and align documents and procedures, and we extended these practices to our suppliers. |
Reducing the risk factors typically associated with our work |
An in-depth analysis of the causes of accidents can identify possible measures for eliminating, mitigating or correcting risk factors by performing organisational, technical or operating solutions on equipment, plants, workplaces, and by implementing certain methods of operation and conduct. The actions and results arising from our accident survey are subjected to further analysis at regular safety meetings, during which staff are informed about the causes of accidents and the measures taken to prevent them. |
“Project Safety” (improvement and prevention plans) |
In 2015, our improvements focused mainly on educating and raising awareness among staff, with a view to promoting safe and careful conduct, on complying with operating and safety procedures and on the correct use of work equipment and protective measures. In addition, we have our “Zero Accidents Award”, whereby employees commit to achieving 365 consecutive days with no accidents at work on their commute. Every year, the winning team receives a significant reward. |
Specialist training |
We provide classroom and on-the-job technical and professional training on these issues, favouring teaching by our own experts and calling on high-quality external training entities and institutions where appropriate. |
Supplier engagement |
Suppliers are evaluated carefully at the qualification stage and then controlled and monitored via feedback and inspections during the work execution phase. Each year, we hold regular workshops with suppliers to present to them the Company’s strategic plans and to share best operating practice in safety, environmental and transparency matters. |
Download XLS (22 kB) |
|
2013 |
2014 |
2015 |
Total employee accidents |
15 |
15 |
22 |
Total contractor accidents |
22 |
16 |
12 |
Employee workplace accidents (no.)
Frequency
Number of non-commuting accidents, resulting in at least one day off work, per one million hours worked.
Employee workplace accidents (no.)
Severity
Number of working days lost, as a result of non-commuting accidents leading to at least one day (calendar days) off work, per one thousand hours worked. Data do not include fatal accidents.
The increase in the frequency of accidents is due, in the main, to gas distribution activities where a greater number of accidents were recorded than in the previous part, also partly as a result of new companies joining the corporate scope.
Cases of employee accidents (%)
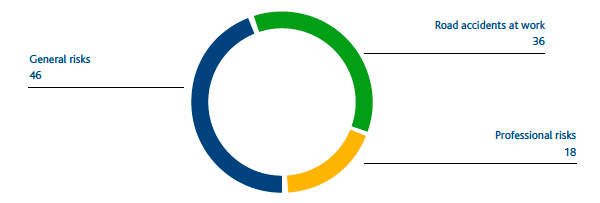
Contractor workplace accidents (no.)
Frequency
Number of non-commuting accidents, resulting in at least one day off work, per one million hours worked.
Contractor workplace accidents (no.)
Severity
Number of working days lost, as a result of non-commuting accidents leading to at least one day off work, per one thousand hours worked.
Download XLS (22 kB) |
|
2013 |
2014 |
2015 |
Training hours delivered |
34,641 |
53,433 |
20,722 |
Participants |
4,255 |
5,886 |
3,629 |
Company |
Grouping |
||
|
|||
Snam Rete Gas |
North District, Stations, Operations (S. Donato), South-West District, Sicily District, North-West District, Staff (S. Donato), West Central District, South-East District |
||
Italgas |
South Distribution Networks Project, North-East District, Rome Gas Distribution, North-West District, Palazzo Uffici HQ in Turin, Sicily District, Central District |
||
Stogit |
Fiume Treste Operating Unit, Crema (HQ), Ripalta-Sergnano Operating Unit, Cortemaggiore-Bordolano Operating Unit, Brugherio-Settala Operating Unit, Minerbio-Sabbioncello Operating Unit |
||
Napoletanagas |
The whole company |
||
Gnl Italia |
The whole company |
||
AES |
The whole company |
Looking after health GRI – G4: LA7
Snam’s employees are not at high risk of contracting occupational illnesses. Those members of staff who are exposed to particular risks receive regular health checks from a doctor-led team based on specific healthcare protocols defined in accordance with the particular risk faced. In addition, specialists will come out to visit them if required. We carry out key surveys in particular working environments designed to monitor microclimatic, biological and physical agents.
We give specific courses of preventive medicine to members of staff who have to travel outside Europe, and we test for alcohol consumption at some sites to check that the ban on drinking in the workplace is being upheld.
Lastly, Snam promotes various employee healthcare initiatives through its corporate welfare system.
Download XLS (22 kB) |
|
2013 |
2014 |
2015 |
Medical visits |
2,674 |
2,630 |
2,766 |
Periodical medical visits |
2,610 |
2,387 |
2,190 |
Diagnostic examinations |
2,989 |
2,203 |
3,827 |
Environmental surveys |
260 |
532 |
245 |
Occupational illnesses diagnosed |
0 |
0 |
0 |
Workplace Health Promotion (WHP)
As part of its Workplace Health Promotion, nine of Snam’s premises in Lombardy have been recognised as “places of work that promote employee healthcare”.
In 2015, the programme focused on “Road safety and sustainable mobility” and “Alcohol and drugs”.
Both initiatives aim to propose and promote practices and habits that, if adopted at work, can also be beneficial in our employees’ personal lives.
“Road safety and sustainable mobility” initiatives
- A new company vehicle usage and management procedure with detailed organisational methods for vehicle use, useful information for drivers, a control and maintenance system to keep the vehicles in good condition and a series of measures for locating vehicles.
- Identification of criteria for purchasing new company vehicles, particularly better safety features and alternation between summer and winter tyres.
- Feasibility of specific training on safe driving.
- Assessment of initiatives to encourage the use of public transport.
- Assessment of special agreements for the purchase of road safety equipment (child seats, helmets and motorcycle armour).
“Alcohol and drugs” initiatives
- A course on the risks of alcohol consumption and infographics aimed at raising employees’ awareness about certain myths regarding alcohol and about the effects and risks arising from the abuse of alcohol.
- New corporate rules banning the sale, administering and consumption of alcohol at workstations, in canteens and anywhere where employees can use a meal voucher, in accordance with our commitment to being an alcohol-free company.
WHP programme phases 2014-16
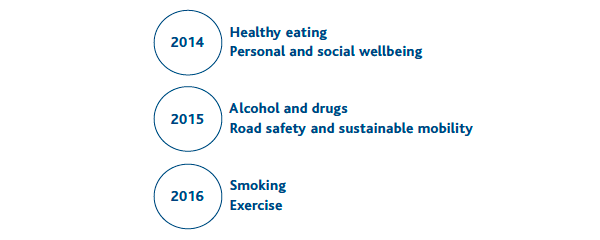
Download XLS (22 kB) |
|
2013 |
2014 |
2015 |
Total number of workers exposed |
4,027 |
3,553 |
4,210 |
Workers who sit at a computer station |
3,270 |
2,712 |
3,574 |
Workers with responsibility in an emergency |
841 |
832 |
862 |
Workers exposed to chemical agents |
326 |
135 |
185 |
Workers responsible for moving heavy loads |
104 |
99 |
147 |
Night workers |
84 |
88 |
77 |
Workers exposed to noise pollution |
19 |
145 |
76 |
Workers at risk for other reasons |
351 |
375 |
357 |